Kontrola kvality produktů je nezbytnou součástí systému správy majetku. V každé fázi výroby existují specifické požadavky na různé typy výrobků, a tedy i na použité materiály. Zpočátku byly hlavními požadavky především přesnost a pevnost, ale s rozvojem průmyslu a komplikací vyráběných zařízení se mnohonásobně zvýšil počet charakteristik, pro které může být odmítnut.
Kontrola funkčních schopností produktů bez jejich zničení je možná díky zdokonalení nedestruktivních testovacích metod. Typy a způsoby jeho provádění vám umožňují vyhodnotit různé parametry, aniž by došlo k porušení integrity produktu, a proto co nejpřesněji. V dnešní době nemá ani jeden technologický proces pro výrobu odpovědných produktů bez dobře vytvořeného řídicího systému právo být zaveden do průmyslu.
Koncept nedestruktivního testování
Tento proces je chápán jako soubortakové zkoušky, kterým je předmět přímo vystaven, při zachování jeho výkonu bez poškození materiálu. Všechny druhy a metody nedestruktivního zkoušení, které dnes existují, mají hlavním účelem zajištění průmyslové bezpečnosti sledováním technického stavu zařízení, budov a konstrukcí. Provádějí se nejen ve fázi výroby (konstrukce), ale také pro včasnou a kvalitní údržbu a opravy.
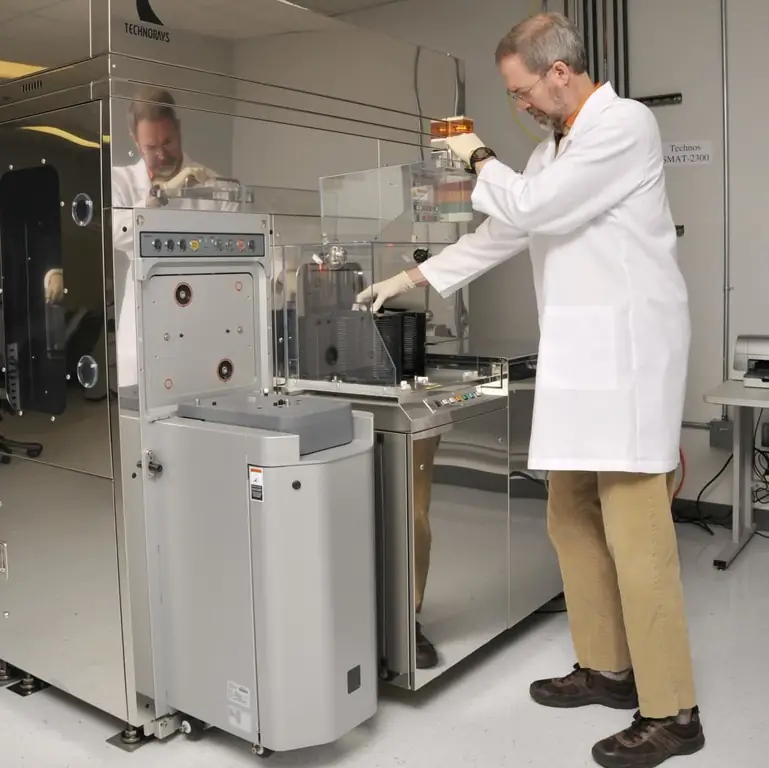
Různými druhy nedestruktivního testování podle GOST lze tedy měřit geometrické parametry výrobků, hodnotit kvalitu povrchové úpravy (například drsnost), strukturu materiálu a jeho chemické složení, přítomnost různých závad. Aktuálnost a spolehlivost získaných dat umožňuje upravit technologický postup a vyrábět konkurenceschopné produkty a také předcházet finančním ztrátám.
Požadavky na kontrolu
Aby byly výsledky všech typů nedestruktivního testování relevantní a účinné, musí splňovat určité požadavky:
- možnost jeho implementace ve všech fázích výroby, během provozu a oprav výrobků;
- kontrola by měla být provedena na maximálním možném počtu daných parametrů pro konkrétní výrobu;
- čas strávený kontrolou by měl být přiměřeně korelován s ostatními kroky ve výrobním procesu;
- spolehlivost výsledků musí být velmi vysoká;
- bypříležitosti pro řízení technologických procesů by měly být mechanizovány a automatizovány;
- spolehlivost zařízení a vybavení používaných při nedestruktivním testování, typy a podmínky jejich použití by se měly lišit;
- jednoduchost metod, ekonomická a technická dostupnost.
Aplikace
Celá řada typů a metod nedestruktivního testování podle GOST se používá pro následující účely:
- detekce závad kritických částí a sestav (jaderné reaktory, letadla, podvodní a povrchová plavidla, kosmické lodě atd.);
- defektoskopie zařízení určených pro dlouhodobý provoz (přístavní zařízení, mosty, jeřáby, jaderné elektrárny a další);
- výzkum metodami nedestruktivního zkoušení kovů, typů jejich struktur a možných vad ve výrobcích ke zlepšení technologie;
- průběžná kontrola nad výskytem závad na jednotkách a zařízeních s nejvyšší odpovědností (např. kotle jaderných elektráren).
Klasifikace typů nedestruktivního testování
Na základě principů fungování zařízení a fyzikálních a chemických jevů jsou všechny metody rozděleny do deseti typů:
- akustické (zejména ultrazvukové);
- vibroakustické;
- s penetrujícími látkami (kapiláry a kontrola netěsností);
- magnetické (nebo magnetické částice);
- optical (vizuální-optický);
- záření;
- rádiová vlna;
- termální;
- elektrický;
- Vířivý proud (nebo elektromagnetický).
Podle GOST 56542 jsou výše uvedené typy a metody nedestruktivního testování dále rozděleny podle následujících znaků:
- zvláštnosti interakce látek nebo fyzikálních polí s řízeným objektem;
- primární parametry poskytující informace;
- získejte primární informace.
Akustické metody
V souladu s klasifikací typů a metod nedestruktivního testování v souladu s GOST R 56542-2015 je tento typ založen na analýze elastických vln, které jsou buzeny a (nebo) vznikají v kontrolovaném objektu. Pokud je použit frekvenční rozsah větší než 20 kHz, může být místo výrazu "akustický" použit výraz "ultrazvukový".
Akustický typ nedestruktivního testování je rozdělen do dvou velkých skupin.
Za prvé - metody založené na vyzařování a příjmu akustických vln. K ovládání se využívá postupné a stojaté vlnění nebo rezonanční kmitání ovládaného objektu. Patří mezi ně:
- Stínová metoda. Přítomnost defektu je detekována v důsledku zeslabení přijímaného signálu nebo zpoždění jeho registrace v důsledku zaoblení defektu ultrazvukovými vlnami.
- Metoda ozvěny. Existence defektu je určena časem příchodu signálu odraženého defektem a povrchy předmětu, což umožňuje určit místo defektu v objemu materiálu.
- Metoda zrcadlového stínu. Jde o variaci stínové metody, která využívá zařízení zecho metoda. Slabý signál je také známkou chyby.
- Impedanční metoda. Pokud je v produktu vada, pak se impedance určité oblasti jeho povrchu snižuje, jako by měknul. To ovlivňuje amplitudu kmitů tyče, mechanické namáhání na jejím konci, fázi kmitů a posun jejich frekvence.
- Rezonanční metoda. Důležité pro měření tloušťky povlaku filmu. Defekt se zjistí pohybem hledáčku po povrchu výrobku, což indikuje zeslabení signálu nebo vymizení rezonance.
- Metoda volných vibrací. V průběhu testování jsou analyzovány frekvence vlastních oscilací vzorku, ke kterým dochází v důsledku dopadu na vzorek.
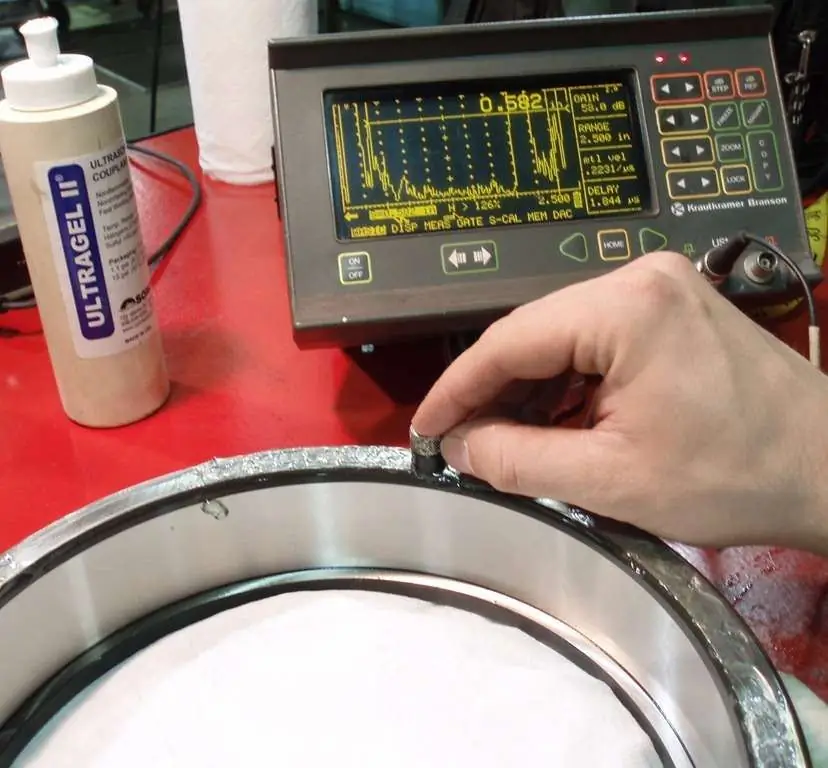
Do druhé skupiny patří metody založené na registraci vln vznikajících v produktech a materiálech:
- Akustická emise. Je založena na registraci vln, které vznikají při vzniku a rozvoji trhlin. Nebezpečné závady vedou ke zvýšení frekvence a amplitudy signálů v určitém frekvenčním rozsahu.
- Metoda šumu a vibrací. Spočívá v pozorování frekvenčního spektra mechanismu nebo jeho částí během provozu.
Typy a metody nedestruktivního testování z výše uvedené klasifikace se používají pro různé účely. Pro stanovení parametrů válcovaného kovu malé tloušťky, pryžových výrobků, sklolaminátu, betonu je nejvhodnější stínová metoda. Jeho podstatnou nevýhodou je nutnost přístupu k produktu ze dvou stran. S jednosměrným přístupem dovzorek může používat metody zrcadlového stínu nebo rezonance. Tyto dva typy se dobře hodí pro nedestruktivní zkoušení svarových spojů a také akustické emise. Impedanční metoda, stejně jako metoda volných vibrací, kontroluje kvalitu lepených a pájených výrobků ze skla, kovu a plastu.
Kapilární metody
Podle klasifikace typů a metod nedestruktivního zkoušení v souladu s GOST R 56542-2015 se kapilární metody vztahují ke zkoušení penetrujícími látkami.
Jsou založeny na pronikání kapek speciálních kapalin, tzv. indikátorů, do dutiny defektů. Metoda se redukuje na čištění povrchu dílu a nanesení penetrační kapaliny na něj. V tomto případě jsou dutiny naplněny, po kterých je kapalina odstraněna z povrchu. Zbytek je detekován pomocí vývojky, která tvoří vzor indikátoru umístění defektů.
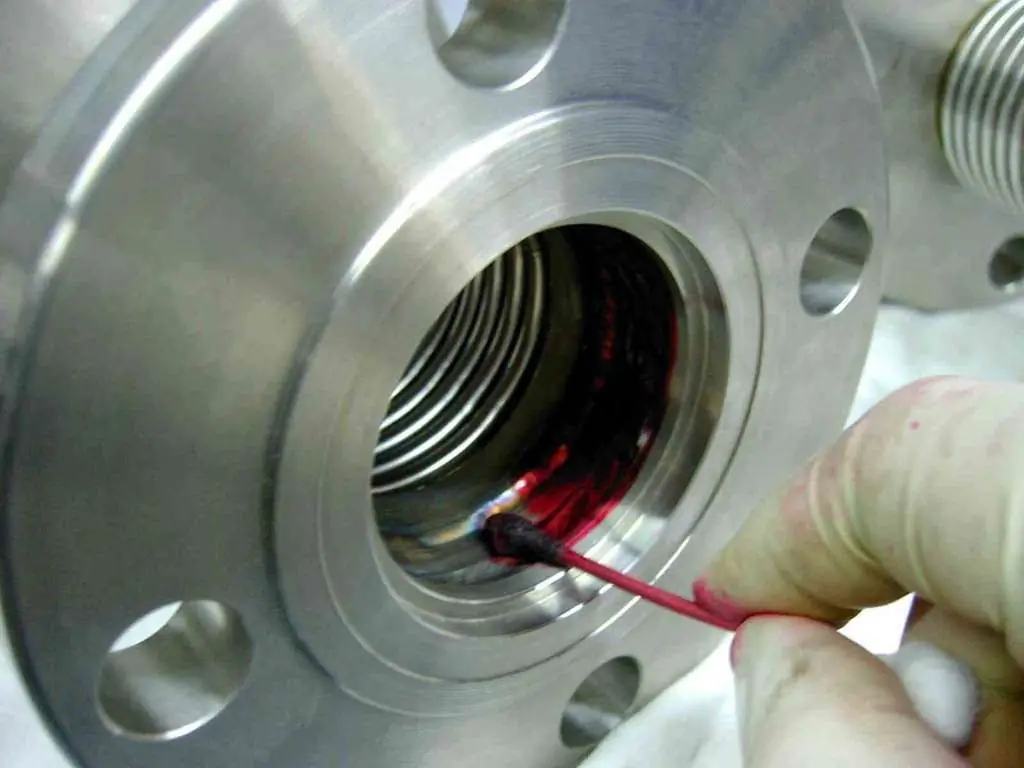
Citlivost kapilárního typu nedestruktivního testování do značné míry závisí na volbě materiálů pro detekci vad, proto je jejich předběžné ověření povinné. Indikátorové schopnosti řešení jsou kontrolovány oproti některým standardním řešením. Bělost vývojek se kontroluje porovnáním s barytovou deskou (standard bělosti).
Výhodou kapilárních metod je možnost jejich použití v polních a laboratorních podmínkách s různou teplotou okolí. Jsou však schopny detekovat pouze povrchové vady s nevyplněnými dutinami. Kapilární metody jsou použitelné prodetekce vad na kovových a nekovových částech různých tvarů.
Magnetické metody
Jsou založeny na registraci magnetických polí vznikajících nad defektem nebo na stanovení magnetických vlastností studovaných produktů. Magnetické metody vám umožňují najít praskliny, vývalky a další vady, jako jsou mechanické vlastnosti feromagnetických ocelí a litin.
Klasifikace nedestruktivních typů a metod kontroly dostupných v GOST umožňuje rozdělení magnetických na následující poddruhy:
- magnetografický (registrace polí se provádí pomocí feromagnetického filmu jako indikátoru);
- magnetická částice (analýza magnetických polí se provádí pomocí feromagnetického prášku nebo magnetické suspenze);
- magnetorezistor (registrace rozptylových magnetických polí se provádí magnetorezistory);
- indukční typ magnetického nedestruktivního testování (monitoruje se velikost nebo fáze indukovaného EMP);
- ponderomotive (zaznamenává se síla vyvolání magnetu z kontrolovaného objektu);
- ferroprobe (na základě měření síly magnetického pole pomocí fluxgate);
- Metoda Hallova efektu (magnetická pole jsou registrována Hallovými senzory).
Optické metody
Typ nedestruktivního testování založeného na působení světelného záření na předmět s registrací výsledků tohoto působení se nazývá optické. Obvykle existují tři skupiny metod:
Vizuál (stejně jako vizuálně-optická metoda) je založen na osobních kvalitách operátora (laborantky): zkušenost, dovednost, vize. Je velmi přístupný a snadno se provádí, což vysvětluje jeho všudypřítomnost. Vizuální kontrola se provádí bez jakýchkoliv optických prostředků. Je účinný na velkých objektech pro detekci hrubých vad, porušení geometrie a rozměrů. Vizuálně-optická analýza se provádí pomocí optických pomůcek, jako je lupa nebo mikroskop. Je méně produktivní, proto se obvykle kombinuje s vizuálním
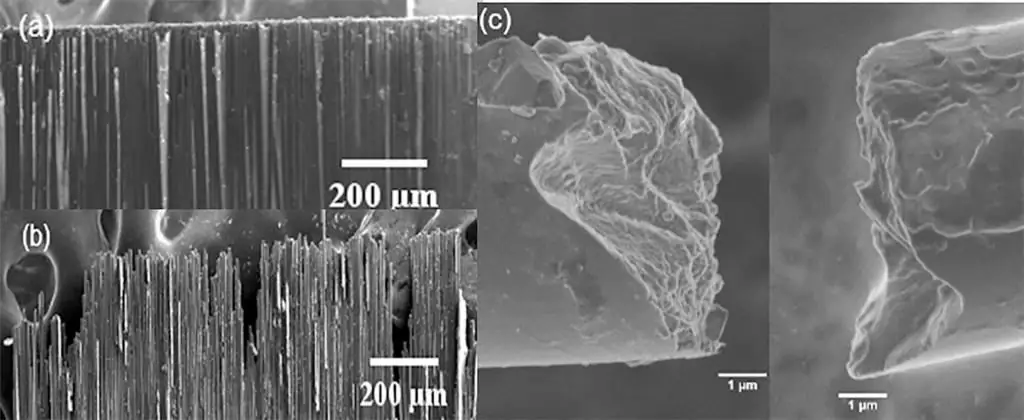
- Fotometrické, denzitometrické, spektrální a televizní metody jsou založeny na přístrojových měřeních a vyznačují se menší subjektivitou. Tyto typy optického nedestruktivního testování jsou nepostradatelné pro měření geometrických rozměrů, povrchových ploch, řízení koeficientu útlumu, hodnocení propustnosti nebo odrazivosti, detekci vad.
- Metody interference, difrakce, fázový kontrast, refraktometrické, nefelometrické, polarizační, stroboskopické, holografické metody jsou založeny na vlnových vlastnostech světla. S jejich pomocí můžete ovládat produkty vyrobené z materiálů, které jsou průhledné nebo průsvitné pro světelné záření.
Metody záření
Na základě účinku ionizujícího elektromagnetického záření na předmět s následnou registrací parametrů této akce a sečtením výsledků kontroly. Pro radiační typ nedestruktivního testování se používají různá záření, která umožňují popsat jejich kvanta těmito fyzikálními veličinami: frekvence, vlnová délka popř.energie.
Rentgenové nebo gama záření, stejně jako toky neutrin, procházející produktem, jsou v různé míře utlumeny v úsecích s defekty i bez nich. Umožňují vám posoudit vnitřní přítomnost nedostatků. Úspěšně se používají ke kontrole svařovaných a pájených švů, válcovaných výrobků.
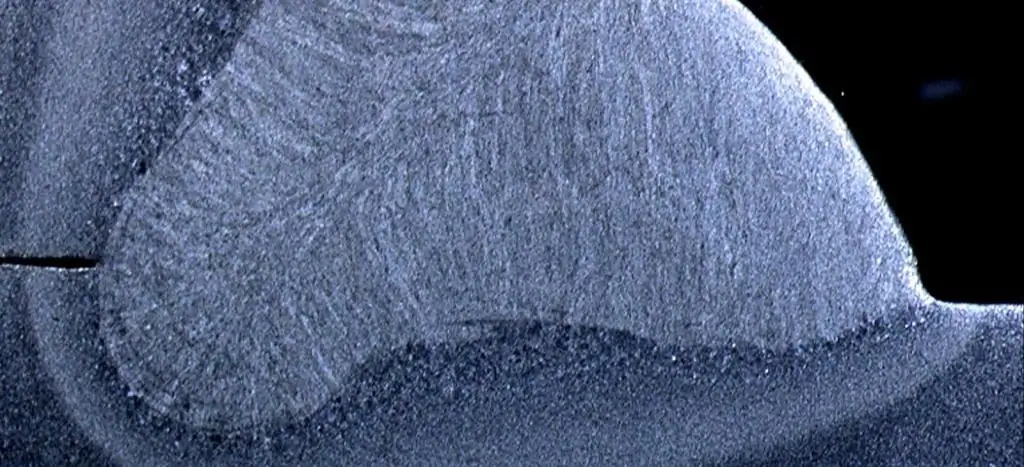
Radiační typy nedestruktivního testování s sebou nesou biologické nebezpečí, působí skrytě. To vyžaduje dodržování organizačních a hygienických norem ochrany práce a bezpečnostních předpisů.
Tepelné metody
Důležitým parametrem je registrace změn vyskytujících se v teplotním nebo teplotním poli analyzovaného vzorku. Pro kontrolu se měří teplota a rozdíly v tepelných charakteristikách objektu.
Termální zobrazení NDT může být pasivní nebo aktivní. V prvním případě nejsou vzorky ovlivňovány vnějšími zdroji tepla a teplotní pole je měřeno na ovládacím mechanismu. Zvýšení nebo snížení teploty na některých místech může naznačovat přítomnost některých nedostatků, jako jsou praskliny v motorech. S aktivním řízením teploty se materiály nebo produkty ohřívají nebo chladí a teplota se měří ze dvou protilehlých stran.
Pro získání přesných a objektivních dat se používají tyto primární měřicí převodníky tepelného záření: teploměry, termočlánky, tepelné odpory, polovodičová zařízení, elektronická vakuová zařízení, pyroelektrické prvky. Často se používají indikátory tepelných polí, které jsoudesky, pasty, filmy látek citlivých na teplo, které se při dosažení určitých teplot mění. Tepelné indikátory tání, tepelné indikátory měnící barvu a fosfory jsou tedy izolovány.
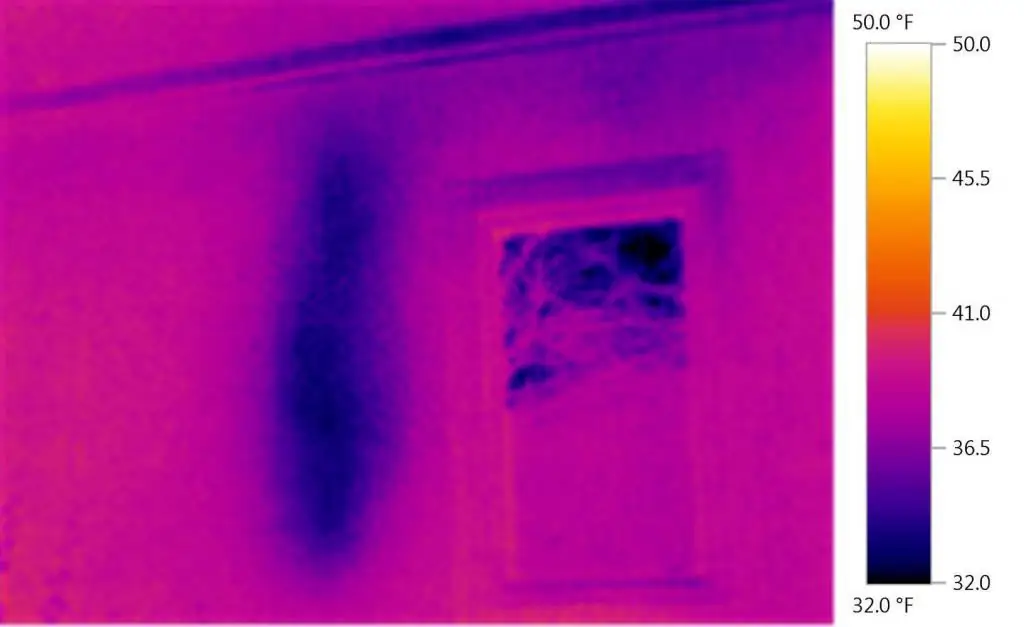
Tepelné metody umožňují pomocí speciálního vybavení měřit fyzikální a geometrické parametry objektů bez dotyku na poměrně velké vzdálenosti. Umožňují také detekovat chemické a fyzikální znečištění, drsnost, povlaky na jejich površích na základě hodnot tepelné emisivity.
Metody detekce netěsností
Podle hlavní klasifikace typů nedestruktivního testování se tato metoda týká testování vzorků s pronikajícími kapalinami. Detekce netěsností odhaluje prostřednictvím defektů ve výrobcích a strukturách průnikem testovaných látek skrz ně. Často označované jako kontrola úniku.
Kapaliny, některé plyny, páry kapalin mohou sloužit jako testovací látky. Podle tohoto parametru se metody kontroly detekce netěsností dělí na kapalinu a plyn. Plyny poskytují větší citlivost, což znamená, že se používají častěji. Také citlivost metody je ovlivněna použitým vybavením. Vakuová technika je v tomto případě nejlepší volbou.
K detekci netěsností jsou zapotřebí speciální zařízení nazývaná detektory netěsností, ale v některých případech jsou vhodné i nepřístrojové metody detekce netěsností. Pro kontrolu této metody se používají následující detektory netěsností:
- Hmotnostní spektrometrie - vyznačuje se nejvcitlivost a všestrannost, umožňuje zkoumat produkty různých rozměrů. To vše vysvětluje jeho široké uplatnění. Ale hmotnostní spektrometr je velmi složitý a objemný přístroj, který ke svému provozu vyžaduje vakuum.
- Halogen, jehož účinek je založen na prudkém zvýšení emisí kationtů alkalických kovů, když se ve zkoušené látce objeví halogeny.
- Bubble - je založena na detekci bublin testovacího plynu uvolněných z netěsnosti během tlakové zkoušky plynu kontrolovaného objektu, s kapalinou nanesenou na jeho povrch nebo ponořenou do nádrže. Jedná se o poměrně jednoduchou metodu, která nevyžaduje složité přístroje a speciální plyny, ale poskytuje vysokou citlivost.
- Manometrické - umožňuje vyhodnotit těsnost testovaného objektu pomocí tlakoměrů, které měří tlak testovacích plynů.
Elektrické metody
Tento typ nedestruktivního testování podle GOST R 56542-2015 je založen na analýze parametrů elektrického pole (nebo proudu) působícího na ovládaný objekt nebo vznikajícího v objektu vlivem vnějšího vlivu.
Informativní parametry v tomto případě - elektrická kapacita nebo potenciál. Pro řízení dielektrik nebo polovodičů se používá kapacitní metoda. Umožňuje analyzovat chemické složení plastů a polovodičů, detekovat v nich nespojitosti a vyhodnocovat obsah vlhkosti sypkých materiálů.
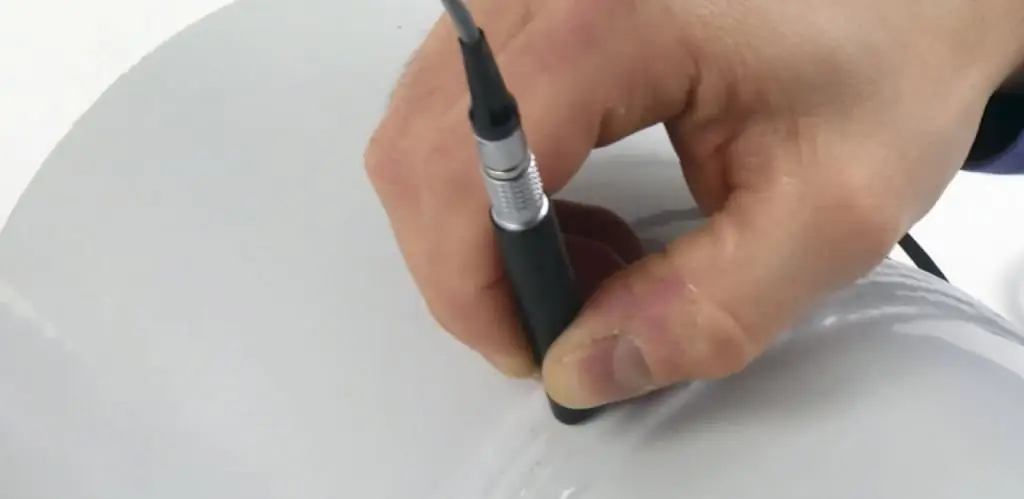
Řízení vodičů se provádí metodou elektrického potenciálu. V tomto případě tloušťka vodivé vrstvy, přítomnost nespojitostíblízko povrchu vodiče je řízeno měřením poklesu potenciálu v určité oblasti.
Metoda vířivých proudů
Má jiný název - metoda vířivých proudů. Je založena na změnách působení elektromagnetického pole cívky s polem vířivých proudů indukovaných touto cívkou v řízeném objektu. Vhodné pro detekci povrchových vad magnetických i nemagnetických dílů a polotovarů. Také vám umožňuje najít praskliny na produktech různých konfigurací.
Metoda vířivých proudů má hodnotu v tom, že ani vlhkost, ani tlak, ani znečištění prostředí, ani radioaktivní záření a dokonce ani kontaminace objektu nevodivými látkami nemají na měřicí signál prakticky žádný vliv. Jeho oblasti použití jsou následující:
- Kontrola lineárních rozměrů výrobků (například průměr tyče, trubky, tloušťka plechu, tloušťka stěny tělesa).
- Měření tloušťky nanesených nátěrů (rozsah od mikrometrů do desítek milimetrů).
- Stanovení odchylek ve složení a struktuře kovů a slitin.
- Stanovení hodnot mechanického namáhání.
Výhody a nevýhody nedestruktivních metod
Navzdory tomu, že oba typy testování, destruktivní i nedestruktivní, mají své klady i zápory, v moderních výrobních podmínkách má to druhé řadu výhod:
- Okamžitě se provádějí testy na produktech, které budou používány v pracovních podmínkách.
- Průzkum lze provést na jakékoli součásti nebo podsestavě určené pro použití v reálném světě, alepokud je to ekonomicky opodstatněné. Často to lze provést, i když se šarže vyznačuje velkými rozdíly mezi díly.
- Můžete otestovat celou část nebo jen její nejnebezpečnější části. V závislosti na výhodnosti vedení nebo technologických podmínkách je lze provádět současně nebo postupně.
- Stejný objekt lze testovat mnoha nedestruktivními testovacími metodami, z nichž každá bude citlivá na určité vlastnosti nebo části součásti.
- Na jednotku lze za provozních podmínek použít nedestruktivní metody a není třeba zastavovat její provoz. Nezpůsobují poruchy a změny v charakteristikách dílů.
- Testování vám umožňuje znovu zkontrolovat stejné díly po libovolné době. To umožňuje navázat spojení mezi provozními režimy a výsledným poškozením a jejich stupněm.
- Nedestruktivní testování umožňuje, aby díly vyrobené z drahých materiálů nebyly poškozeny.
- Zkoušky se zpravidla provádějí bez předběžné úpravy vzorků. Mnoho analytických zařízení je přenosných a rychlých a často automatizovaných.
- Náklady na nedestruktivní testování jsou nižší než náklady na destruktivní metody.
- Většina metod je rychlých a vyžaduje méně člověkohodin. Takové metody by se měly používat ke stanovení kvality všech podrobností, pokud jsou jejich náklady nižší nebo srovnatelné s náklady na provedení destruktivního průzkumu.pouze malé procento dílů v celé dávce.
Nedestruktivní testovací metody nemají tolik nevýhod:
- Obvykle se analyzují nepřímé vlastnosti, které nemají přímou souvislost s hodnotami během provozu. Pro spolehlivost výsledků je zjištěn nepřímý vztah mezi získanými údaji a provozní spolehlivostí.
- Většina testů neukazuje životnost objektu, ale dokáže pouze sledovat procesy destrukce.
- K dešifrování a interpretaci výsledků analytické práce je také nutné provést stejné studie na speciálních vzorcích a za zvláštních podmínek. A pokud relevantní souvislost mezi těmito testy není zřejmá a prokázaná, pak s tím pozorovatelé nemusí souhlasit.
Analyzovali jsme typy nedestruktivního testování, jeho vlastnosti a nevýhody.